Nano-indentation
Principle
Nano-indentation is a mechanical characterization technique that involves pressing a tip with a controlled geometry into a material. By recording the applied force as a function of the indentation depth, mechanical properties at the micrometer scale, such as hardness and Young’s modulus, can be evaluated using the Oliver and Pharr method [1]. The indentation depth ranges from a few hundred nanometers to several micrometers. The upper depth limit is determined by the size of the phase to be analyzed, which must be at least 10 times larger than the indentation imprint. The lower depth limit is constrained by the material’s roughness, which must be at least 20 times smaller than the indentation depth and suitable for the size of the phase to be measured and to that of the phases at the lower scale. [2].
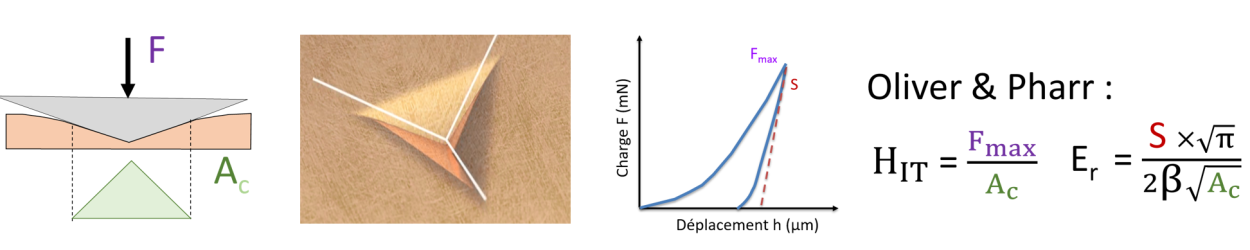
Sample preparation
To achieve an acceptable roughness level, meticulous sample preparation is crucial. The sample is first cut using a micro-cutting machine and then embedded in epoxy resin. It is subsequently polished with silicon carbide (SiC) abrasive papers of progressively finer grit sizes. Final polishing with diamond powder ensures minimal roughness. The resulting roughness is precisely measured using the Atomic Force Microscope (AFM) installed on the same frame as the indentation system.

The nano-indenter device
The Navier laboratory’s nano-indenter is an NHT² model (Anton Paar) with a maximum force of 500 mN, a maximum depth of 200 µm, and a maximum loading rate of 10 N/min. It is installed in a climate-controlled chamber (temperature: 10 to 40 °C, relative humidity: 20 to 95%) and mounted on a vibration-isolated slab with an air compression system.
The sample can be positioned with micrometric stages (X, Y, Z), allowing movement between the optical microscopy, AFM, and nano-indentation modules. A tilting stage ensures parallel alignment between the sample and the modules. Automated indentation grids can be configured to perform tens or even hundreds of indentations in sequence.
The system allows control in either force or displacement mode and supports dynamic indentations (sinus mode). This mode enables the characterization of Young’s modulus and hardness as a function of indentation depth, as well as viscoelastic properties such as storage modulus (E’) and loss modulus (E").
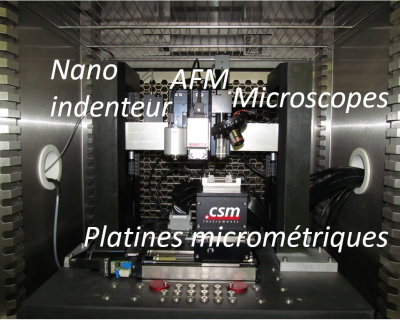
Studies conducted at the laboratory
– Modeling of mechanical characterization by indentation: analysis of hardness influenced by geometric changes during indentation using a limit analysis approach [3].
– Recycled aggregate concrete: statistical analysis of local elastic properties of aggregates and cement paste (including ITZ) [4].
– Rock studies and homogenization: coupling of indentation and SEM-EDS analysis for source rocks [5] and carbonates [6].
– Early-age cement: dynamic indentation to study cement setting (ongoing).
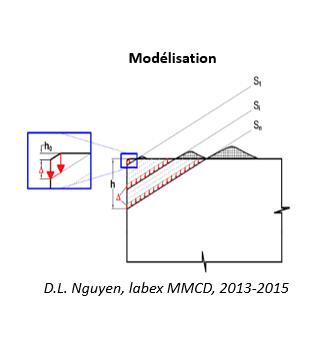
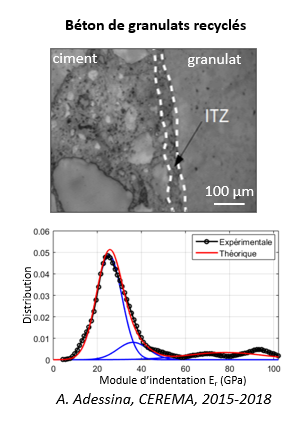
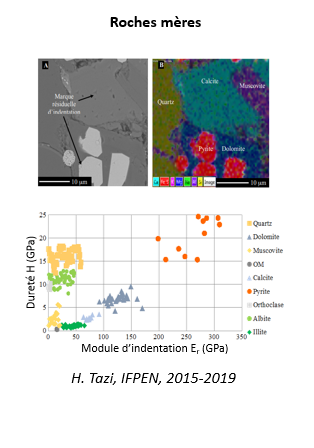
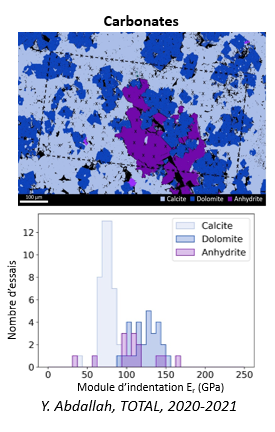
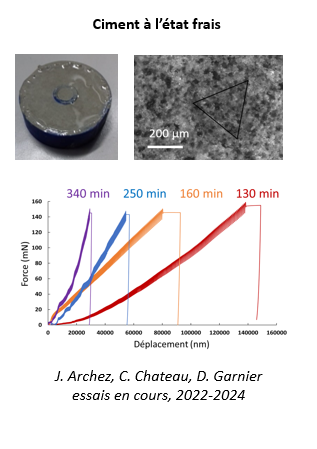
Références
[2] ISO 14577-4:2016 Matériaux métalliques – Essai de pénétration instrumenté pour la détermination de la dureté et de paramètres des matériaux – 2016.
[3] Dac Loi Nguyen, “Simulation numérique d’un essai de nano-indentation sur un matériau de critère de résistance elliptique axisymétrique", Thèse de doctorat, 2015.
[4] A. Adessina, “Caractérisation expérimentale et modélisation multi-échelle des propriétés mécaniques et de durabilité des bétons à base de granulats recyclés, thèse de doctorat, 2018.
[5] H. Tazi, “Propriétés élastiques et anisotropie des roches mères : approche expérimentale multi-échelle et modélisation par milieu effectif", Thèse de doctorat, 2019.
[6] Y. Abdallah et al., “Linking elastic properties of various carbonate rocks to their microstructure by coupling nanoindentation and SEM-EDS”, International Journal of Rock Mechanics and Mining Sciences, 170, 105456, 2023.