Our research group studies the mechanical and physical properties of colloidal suspensions and pastes at the particle scale, from the ideal case of hard spheres to more complex cases involving rod-like particles (two-dimensional analogues of clay particles) and the addition of surfactants and polymer interacting with the particles. We combine numerical simulation and experimental tools, e.g. the optical tweezers setup. We also examine the extrudability and three-dimensional printing of these materials at the macroscopic scale.
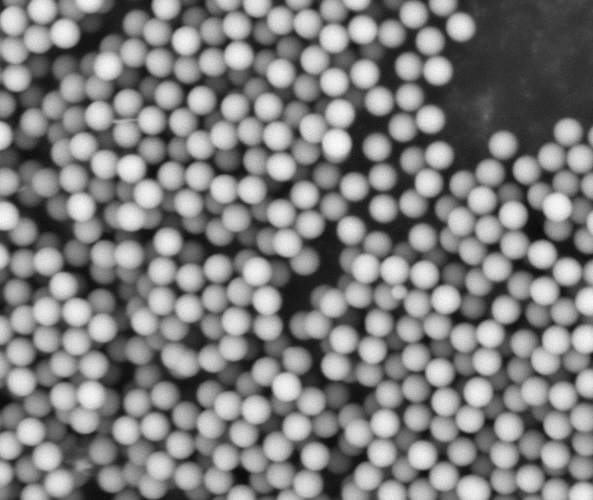
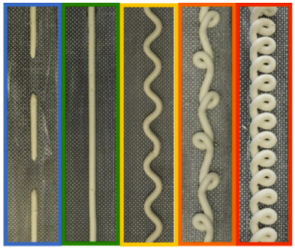
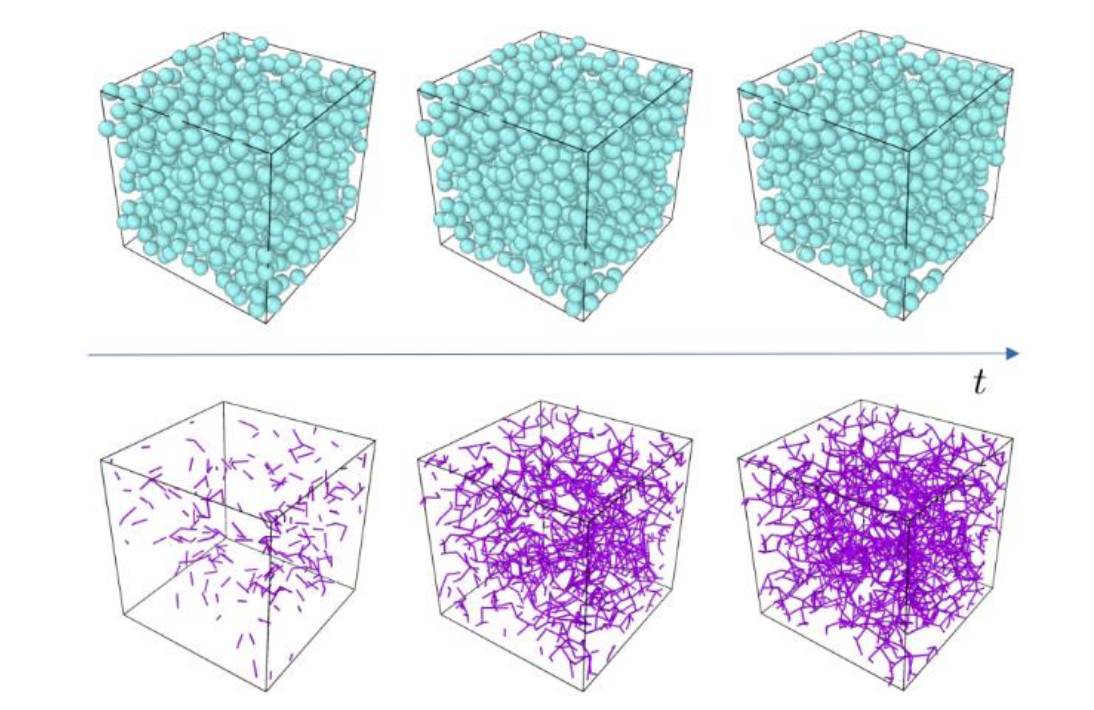
Rheology and aging of colloidal suspensions
X. Chateau, J. Goyon-Trohay, A. Lemaître, A. Aubel (PhD), C. Veillon (PhD)
Collaborations : E. Furst (U. Delaware)
Suspensions of micron-sized particles have complex rheological characteristics which typically include a yield stress under which they do not flow, the origin of which being unclear. We have evidenced that thixotropy in these materials occurs without any microstructural changes in these materials. Using a three-point flexural test on particle rods built using optical tweezers, we have shown that contacts between particles resist sliding and rolling motion. This resistance increases with the age of the contact. We have successfully described the macroscopic rheological properties of these materials from the contact properties between particles only using scalar functions of the suspension microstructure.
We have then showed that adding a non-ionic surfactant to the suspension drastically modifies the rolling properties of the interparticle contacts and the bulk rheology of the suspension. The change in contact properties is attributed to surfactant adsorption at the particle surface, which transforms an adhesive contact resisting rolling motion into a non-adhesive contact. As in the case of the clean silica suspension, the excellent quantitative agreement between bulk tests and particle beam tests demonstrates that contact properties between grains control the global properties of the suspension. These results should lead us to reconsider our understanding of thixotropy in dense colloidal suspensions, paving the way to future advances in their formulation.
Credits : École Nationale des Ponts et Chaussées & Ingenius, the digital digest of the École.
References
- Contact and macroscopic aging in colloidal suspensions, F. Bonacci, X. Chateau, E. M. Furst, J. Goyon and A. Lemaitre, Nature Materials, 19, 775-780 (2020).
- Yield stress aging in attractive colloidal suspensions, F. Bonacci, X. Chateau, E. M. Furst, J. Goyon and A. Lemaitre, Physical Review Letters 128, 018003 (2022).
- Adjuvantation de suspensions modèles : caractérisation multi-échelle, Antoine Aubel, PhD thesis (2023).
3D Printing of Yield-Stress Fluids
P. Coussot, A. Geffrault (PhD)
Collaboration : H. Bessaies-Bay, N. Roussel (CPDM)
Three-dimensional printing of yield-stress fluids (which only flow above a critical applied shear stress) has unlocked new possibilities in the construction, food and healthcare sectors. Standard printing techniques consist in extruding then depositing a filament of yield-stress fluid atop the previous layer of fluid. One major difficulty is that instabilities may arise during deposition, with a catastrophic impact on the final three-dimensional structure.
We have shown that these instabilities can be simply predicted as a function of the material properties and the printing parameters. To this end, we have studied the filament deposition of a model yield-stress fluid and examined the impact of the material yield stress, the distance between the extrusion head and the substrate, the extrusion speed, the head diameter and the printing speed. We have observed a broad range of patterns: drops, discontinuous lines, straight lines, meanders, alternated loops and single-sided loops. We have delineated the boundaries between these regimes and explained them using theoretical arguments, which led us to formulate stability regions based on the aforementioned system parameters.
In a similar study, we have studied in detail the process leading to the formation of a fluidised region next to the ‘necking’ between two yield-stress drops. Analysing our results, we have developed an original technique to measure the elongational rheological properties of yield-stress fluids and a simple technique to determine the yield stress of these materials from the mass of the detached drops.
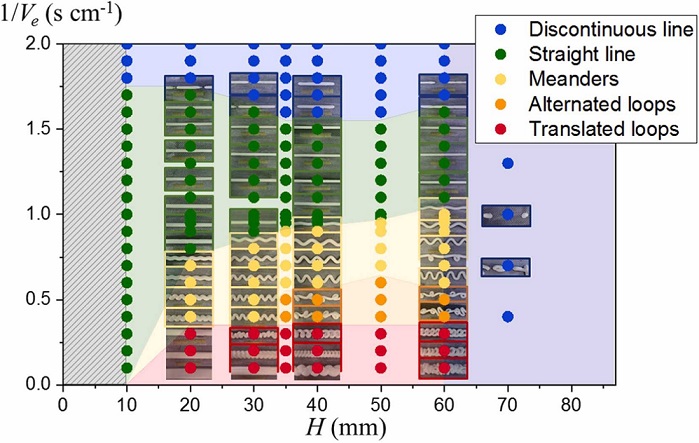
Phase diagram of the various morphologies of a yield-stress filament printed from an extrusion head. We print a kaolin paste (yield stress 300 Pa) as a function of the extrusion speed Ve and the vertical distance between the extrusion head and the substrate. The printing speed (translation of the extrusion head) is set to 1 cm/s.
References
- Printing by yield stress fluid shaping, A. Geffrault, H. Bessaies-Bey, N. Roussel, P. Coussot, Additive Manufacturing 75, 103725 (2023)
- Instant yield stress measurement from falling drop size: The “syringe test”, A. Geffrault, H. Bessaies-Bey, N. Roussel, P. Coussot, Journal of Rheology 67, 305-314 (2023)
Numerical Methods for Colloidal Suspensions
A. Lemaître, F. Puosi, D. Richard (Postdoc), P. Sanchez-Moreno Royer (PhD)
Many materials from civil engineering and the environmental sector are dense colloidal pastes of varied shapes and sizes, from tens of nanometers to a few microns. Despite the enormous research efforts undertaken to master their formulation and their placement and shaping, we only have a very limited understanding of the physical mechanisms governing the inter-particle interactions. Discrete numerical simulations are indispensable to identify the relevant physical mechanisms in these systems and guide the interpretation of experiments.
We have started developing numerical models (since Francesco Puosi joined us in December 2022) able to take into account the richness and the complexity of inter-particle interactions. We wish to understand the elementary physical mechanisms — at the particle scale — that determine the macroscopic behaviour of these systems. We are particularly interested in suspensions of adhesive spheres and an explicit model of clays taking into account the geometry (rod-like or platelet-like) of these particles to compute their exact interaction.
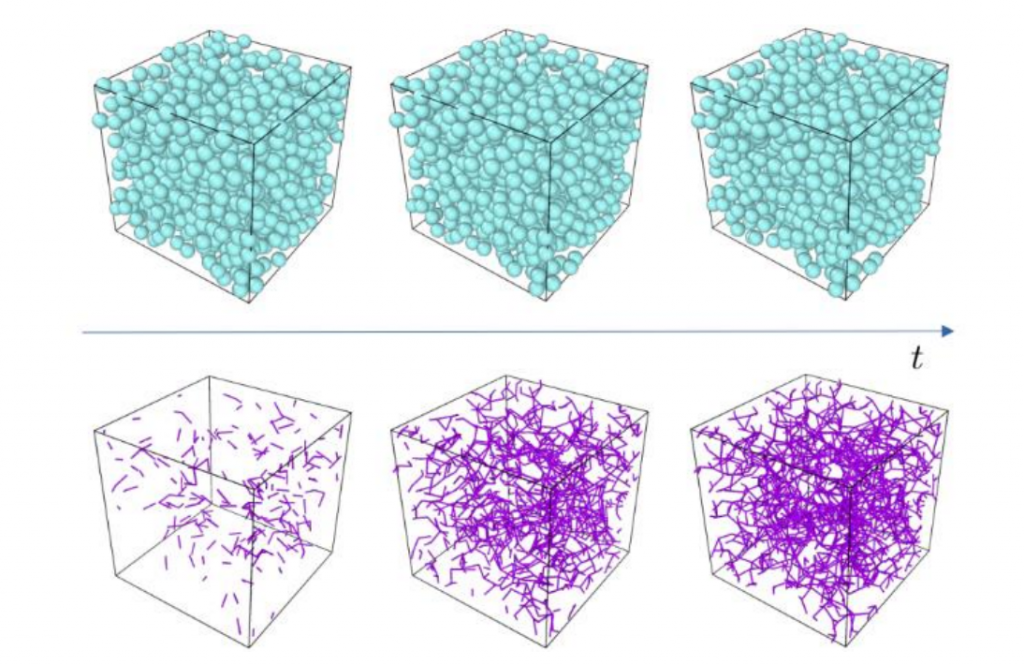
Numerical simulation of the aging of an adhesive colloidal suspension.