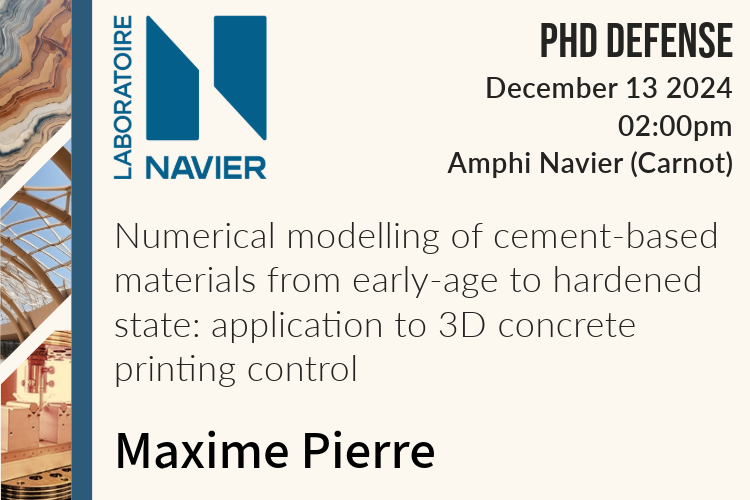
PhD Defense – Maxime Pierre
- Post by: Mathias Lebihain
- 3 December 2024
- No Comment
Maxime Pierre, a PhD candidate in the Geotechnics, MSA, and Multiscale teams, will defend his dissertation titled “Numerical modelling of cement-based materials from early-age to hardened state: application to 3D concrete printing control” on Friday, November 13, at 2:00 PM, in the Navier amphitheater.
Composition du jury :
- Bernhard Pichler (TU Wien) – Reviewer
- Arnaud Perrot (Université de Bretagne Sud) – Reviewer
- Pietro Lura (ETH Zürich) – Examinator
- Rob Wolfs (TU Eindhoven) – Examinator
- Sylvie Granet (EDF R&D) – Examinator
- Siavash Ghabezloo (ENPC) – Thesis director
- Patrick Dangla (UGE) – Co-supervisor
- Jean-François Caron (ENPC) – Co-supervisor
- Matthieu Vandamme (ENPC) – Co-supervisor
- Romain Mesnil (ENPC) – Co-supervisor
Abstract
Show the abstract
3D concrete printing is a technology on the rise, promising to tackle two of the main issues in the construction industry today: low productivity and high environmental impact. Selective deposition of the material allows for optimal usage, thus reducing overall material consumption compared with traditional casting, while also alleviating the need for skilled labour. However, this new technology is faced with many critical issues stemming from the elimination of the formwork. Without the mechanical barrier of the formwork preventing fresh cement-based material from flowing out, the 3D-printed material must be able to sustain its self-weight at the very early age. The formwork also constitutes a protective layer against the environment, namely preventing drying from the concrete surface. In its absence, shrinkage cracking and other durability issues become of prime importance.
The success of 3D printing with cement-based materials relies until now mainly on the practical knowledge of highly-skilled operators. To improve the consistency of the tech.nology and enable a wider adoption in the industry, adequate modelling tools are required with the ability to analyse the feasibility and estimate the durability of 3D printed ob.jects. The goal of the present work is to develop a comprehensive framework capable of serving this purpose. It is focused on two aspects: constitutive modelling at the scale of the material and structural-scale simulation of 3D printed objects.
The proposed constitutive model constitutes an extension of previously developed poromechanics based models for oil-well cementing purposes. The improvements include thermal couplings, viscoplasticity, and taking into account additional mechanisms relevant to materials and load cases in the context of 3D printing, such as the interaction between partial saturation and hydration kinetics. This model is fully encompassed in a general thermodynamical theoretical framework. It is validated against existing experimental results on early-age cement pastes involving hydromechanical couplings during hydration. The model can account for the effect of previous stress history on the material behaviour at a given time.
Simulating 3D concrete printing also requires modelling of the printing process itself. To this end, a full simulation framework was developed based on open-source bricks. It includes a meshing tool which produces meshes based on robot printing paths associated with an FEM solver to create a “digital twin” of the printing process. Indeed, during printing, material is continuously being deposited so that the geometry of a print-piece is evolving in time, which is reproduced in the simulation. Process-related parameters, such as layer-pressing, are also taken into account.
Using this framework, failure during the printing of complex geometries can be estimated, be it from plastic collapse or from elastic buckling. Beyond the printing phase alone, the thermo-hydro-chemical coupling mechanisms linked with evaporation at the surface of the fresh mortar can also be simulated to investigate the so-called “cold-joint” effect at interfaces or the gradient of hydration observed in the width of a layer. Ultimately, we show how an optimisation procedure can be integrated into the simulation framework to tailor some process parameters such as printing speed ahead of printing. In that way, it is possible to modulate process parameters in the time frame of printing to maximise productivity while steering away from the risk of collapse.